RJ Lee Group 12 min read
Testing Concrete for Chloride Penetration
Contributors
RJ Lee Group
Subscribe to our newsletter
One of the most common causes of structural concrete deterioration is corrosion of the reinforcing steel within the concrete member. Engineers dealing with concrete exposed to chlorides are likely asked to answer these questions:
- How resistant is the concrete to chloride ingress?
- To what degree have chlorides infiltrated the concrete?
- What is the likelihood that the reinforcing steel is undergoing corrosion?
- If there is corrosion occurring, what are the rate and extent of corrosion and its effect on service life?
- If not, what is the likelihood that chlorides will cause corrosion in the future?
Different tests are needed to help answer each of these questions. Engineers may use these test results to qualify a concrete mixture for use on a project, to accept concrete that has been placed, as inputs for service life models such as Life 365 and STADIUM®, or to develop repair strategies for structures. This article focuses on tests to directly answer the first two questions, which in turn can help answer the remaining three.

Resistance to Chloride Ingress
The high pH of concrete permits the formation of a corrosion-resistant passive oxide layer on the surface of the reinforcing steel. This passive layer can break down and enable active corrosion if the concrete is carbonated, decreasing the pH, or if sufficient chloride ions penetrate the concrete and attack the passive layer. Water containing aggressive chloride ions can penetrate concrete through larger capillary pores and cracks and through diffusion through smaller pores in the paste. The ion-rich fluid in these pores that facilitates chloride ingress is known as the pore solution and its electrical properties are key to some tests for chloride resistance in concrete.
Transport by diffusion is driven by chlorides moving from areas of high chloride concentration (e.g. seawater or deicing salts at the surface) to a low concentration in the interior of the concrete. Concrete with a high water-to-cementitious materials ratio (w/cm) or which is inadequately cured and hydrated will be more porous and offer less resistance to chloride ingress, while good curing and a lower w/cm will lead to the development of a microstructure with smaller and disconnected pores that offer more resistance to chloride ingress.
Chloride diffusion tests are designed to yield a property known as the apparent diffusion coefficient, which describes how easy or hard it is for chlorides to penetrate a concrete sample primarily by diffusion rather than capillary transport. Diffusion tests include ASTM C15561 and NT BUILD 4432. In these tests, water-saturated concrete is exposed on one surface (ideally with no prior chloride exposure) to a solution of sodium chloride for at least 35 days. The concrete is then analyzed for chloride content versus depth. Using Fick’s Second Law of Diffusion and a nonlinear regression analysis, a curve is fit to the data and the apparent diffusion coefficient is calculated, as shown in Figure 1. A lower coefficient indicates greater resistance to chloride ingress.
Electrical methods such as ASTM C12023 (sometimes called the Rapid Chloride Permeability Test, or RCPT) and surface resistivity (AASHTO T 3584) provide measurements governed by the pore structure and pore solution composition. ASTM C1202 measures the charge passed, in Coulombs, through a concrete disc that is placed between conductive solutions of sodium chloride and sodium hydroxide. Less charge passed correlates to greater resistance to chloride ingress. Surface resistivity measures the electrical resistivity (or in ASTM C18765, the inverse, conductivity) of the concrete between electrical probes; higher resistivity correlates to greater resistance to chloride ingress. Electrical tests are much faster than diffusion tests, but results can be skewed by the presence of conductive materials in the concrete such as steel fibers or reinforcing steel, prior chloride exposure, or some chemical admixtures. These tests do not measure the actual movement of chloride ions.
NT BUILD 4926 combines features of both electrical and diffusion tests, using an electric current to force the migration of chlorides from an anolyte solution into a concrete sample. The applied voltage and temperature of the solution are monitored during the test. Afterward, the sample is sliced open, and the chloride penetration depth is determined by applying silver nitrate to the freshly cut face, which reacts with chlorides to produce a white silver chloride deposit. This test can be completed in one to four days and yields a property known as the non-steady-state migration coefficient, which is similar to the apparent diffusion coefficient.
Diffusion and migration coefficients are used in computational service life models to predict how long it will take for sufficient chlorides to reach the reinforcing steel and initiate corrosion. This can be done for both new and existing structures. Measurements of electrical properties can be correlated to chloride diffusion and migration coefficients. Because electrical tests require less time and effort to conduct, they are more commonly implemented in project specifications to qualify mixture designs or accept concrete that has been placed.
Recent work has sought to use a concept called the Formation Factor, or F-Factor, to estimate the resistance to chloride ingress of concrete7. The formation factor is based on a petroleum geology concept called Archie’s Law and is the ratio of the resistivity of saturated concrete to the resistivity of its pore solution. Concrete resistivity (or conductivity) is measured as described above, while pore solution resistivity generally must be estimated. The F-Factor has been incorporated into the AASHTO PP 848 standard for Performance Engineered Mixtures an alternative to using ASTM C1202 or diffusion tests for specifying chloride-resistant concrete.
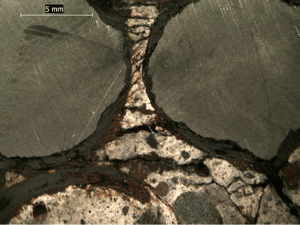
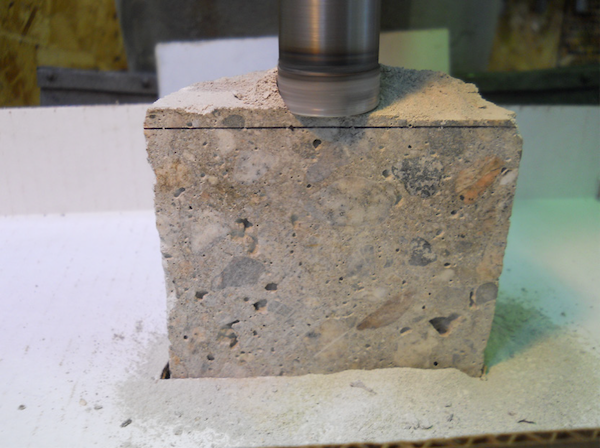
Quantifying Chlorides in Concrete
When a concrete structure has been exposed to chlorides in service, engineers evaluating the remaining service life or developing repair strategies should quantify the degree of chloride penetration. A series of powder samples obtained at multiple depth intervals from a drilled core specimen, or from a smaller drilled hole, are used to develop a chloride depth profile. The mass percentage of acid-soluble chlorides in each powder sample is measured following ASTM C11529 and plotted against depth from the chloride-exposed surface, as shown in Figure 2. This information can be used to determine if sufficient chlorides to initiate corrosion are approaching or have reached the depth of the reinforcing steel. It can also be combined with information about the age of the structure and its transport characteristics (i.e. resistivity or diffusion coefficient) to predict the remaining service life and select appropriate repair strategies.
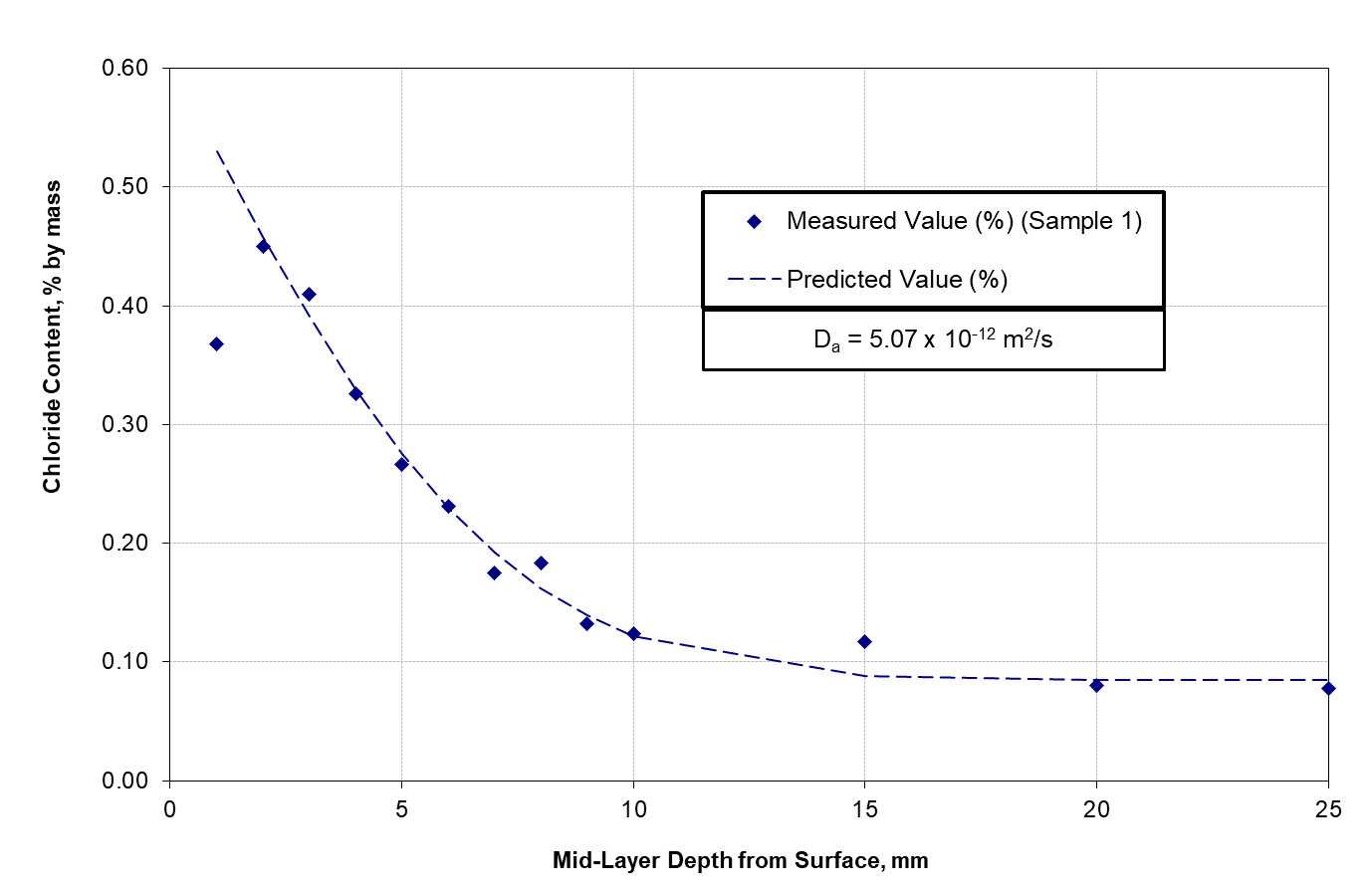
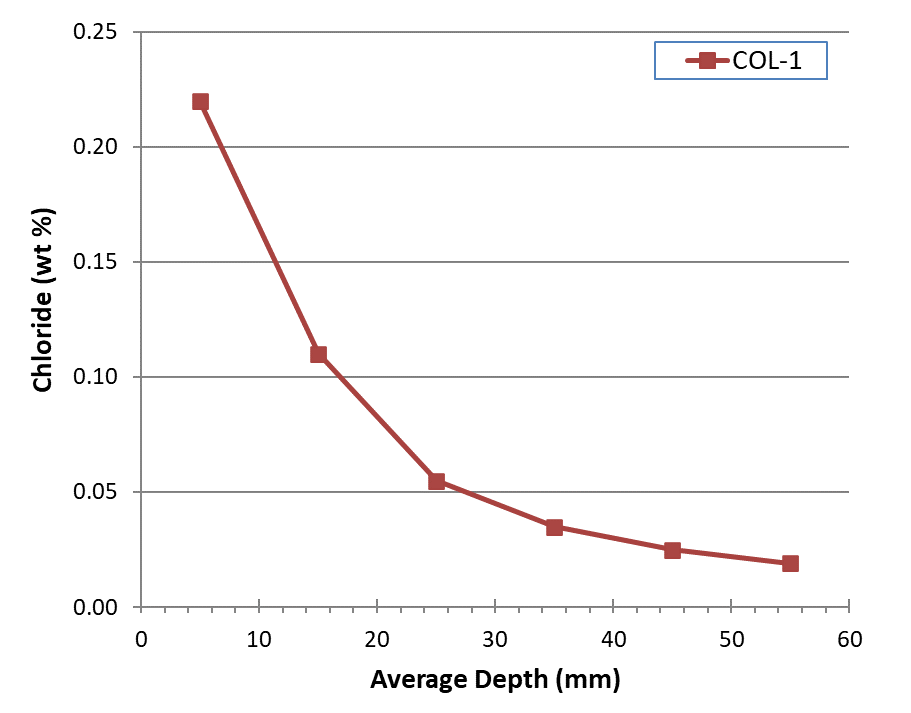
.png?width=911&height=713&name=image2-2%20(1).png)
References
1ASTM C1556-11a(2016), Standard Test Method for Determining the Apparent Chloride Diffusion Coefficient of Cementitious Mixtures by Bulk Diffusion, ASTM International, West Conshohocken, PA, 2016
2NT BUILD 443, Concrete, hardened: Accelerated Chloride Penetration, Nordtest, Espoo, Finland, 1995.
3ASTM C1202-19, Standard Test Method for Electrical Indication of Concrete’s Ability to Resist Chloride Ion Penetration, ASTM International, West Conshohocken, PA, 2019.
4AASHTO T 358, Standard Method of Test for Surface Resistivity Indication of Concrete’s Ability to Resist Chloride Ion Penetration, American Association of State Highway and Transportation Officials, Washington, DC, 2021.
5ASTM C1876-19, Standard Test Method for Bulk Electrical Resistivity or Bulk Conductivity of Concrete, ASTM International, West Conshohocken, PA, 2019.
6NT BUILD 492, Concrete, mortar and cement-based repair materials: Chloride migration coefficient from non-steady-state migration experiments, Nordtest, Espoo, Finland, 1999.
7http://research.engr.oregonstate.edu/concreteff/litarature.html
8AASHTO PP 84, Standard Practice for Developing Performance Engineered Concrete Pavement Mixtures, American Association of State Highway and Transportation Officials, Washington, DC, 2020.
9 ASTM C1152/C1152M-20, Standard Test Method for Acid-Soluble Chloride in Mortar and Concrete, ASTM International, West Conshohocken, PA, 2020.
Referenced Standard Test Methods provided by RJLG:
- ASTM C1152 Standard Test method for Acid-Soluble Chloride in Mortar and Concrete
- ASTM C1218 Standard Test Method for Water-Soluble Chloride in Mortar and Concrete
- ASTM C1202 Standard Test Method for Electrical Indication of Concretes Ability to Resist Chloride Ion Penetration
- ASTM C1556 Standard Test Method for Determining the Apparent Chloride Diffusion Coefficient of Cementitious Mixtures by Bulk Diffusion
Associated RJ Lee Group Services:
- Concrete Materials
- Concrete Petrography
- Corrosion Testing
- Inorganic Chemistry for Chloride and Sulfur: IC, ICP-AES, LECO
- Failure Analysis
- Metals and Alloys
Share this blog